Reinforced embankments with vertical concrete facing
2020
BRAZZAVILLE - BRAZZAVILLE - Congo
Etat Congolais
CONSTRUCTION DE LA ROUTE DE LA CORNICHE DE BRAZZAVILLE
Problem
The extension project of the Corniche road in Brazzaville is part of a larger construction contract involving urban developments in the Bacongo and Makélékélé neighborhoods. The extension of the Corniche road to a 2×2 lane configuration covers approximately 5 kilometers between the Djoué Bridge and the Case de Gaulle. The route, on a slope, runs along the Congo River and requires the construction of several support structures. The technical solution specified in the contract was a patterned concrete L-wall with reinforcement of the embankment using geotextile boudins. Maccaferri proposed an alternative solution with a reinforced embankment featuring patterned concrete facing Macres®, which was favored by the company as it met the technical and aesthetic requirements of the project while significantly saving installation time and providing overall cost savings.
Solution
The Paraweb® MD45 geoband reinforcements were used and perfectly adapted to the intermediate material embankments (Type 3 according to NF EN 14475). Depending on the heights and sections, the bands had varying lengths between 4 and 11 meters. At the head of the wall, the presence of a 1.30-meter-deep channel 2 meters from the facing did not allow for the deployment of the upper bands. Therefore, the head scales were connected to a concrete beam poured parallel to the facing using waiting iron bars placed during prefabrication. Fifteen walls, with a total surface area of approximately 6,000 square meters and a maximum height of 8.50 meters, were constructed in six different sectors. The Macres® solution offers several advantages:-Uniformity and flexibility of the structure: The embankment and facing form a homogeneous structure, absorb settlements without damage, and perform well under seismic loads.-Reliability of Paraweb® polymer reinforcements, which are corrosion-resistant and have a lifespan of 120 years.-Speed and ease of execution.-Cost-effective solution due to reduced steel and concrete consumption and a decrease in the number of transportation trips to supply the construction site.
Used Products
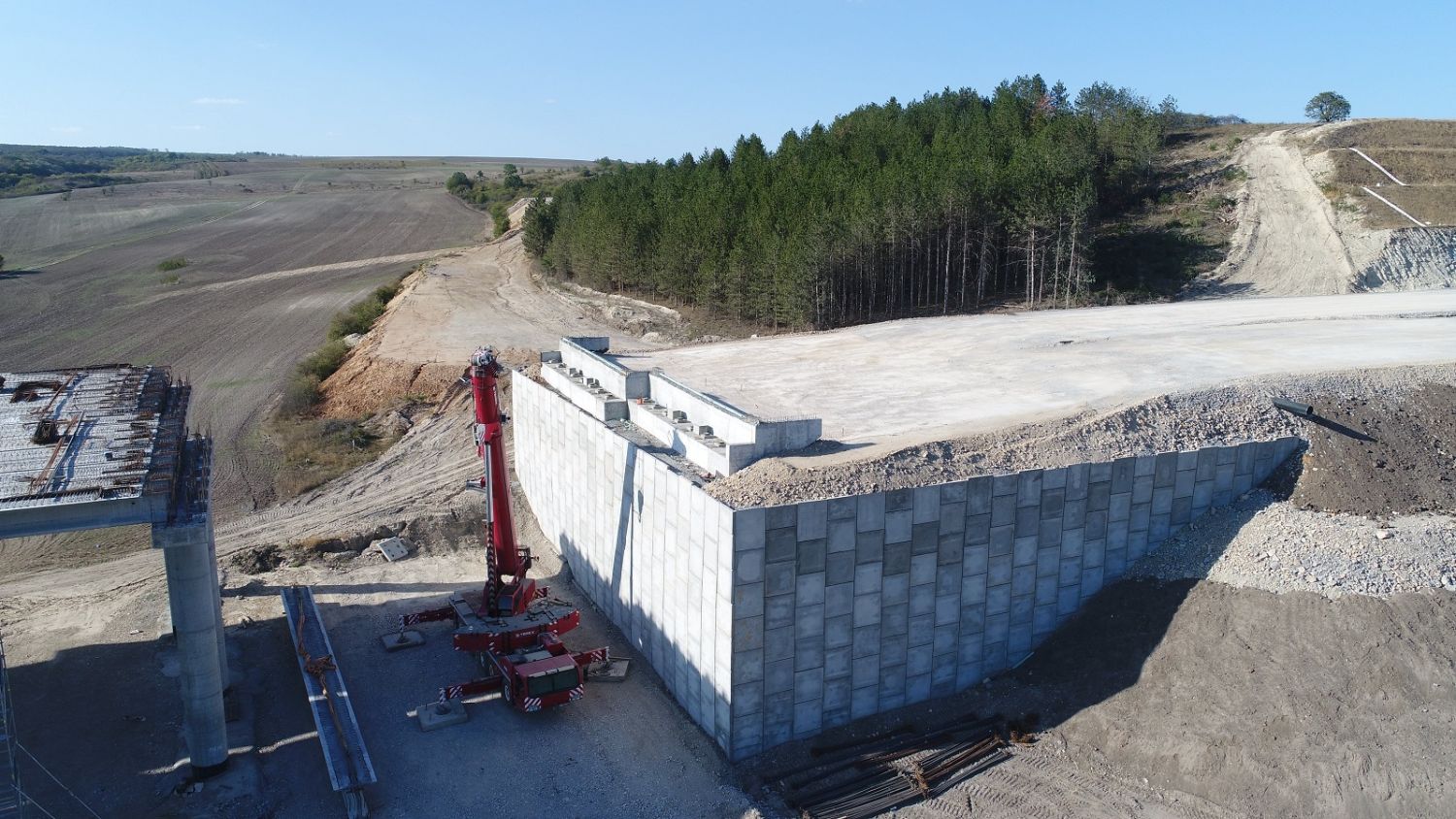